CNC Machining Parts Factory: The Heart of Precision Engineering
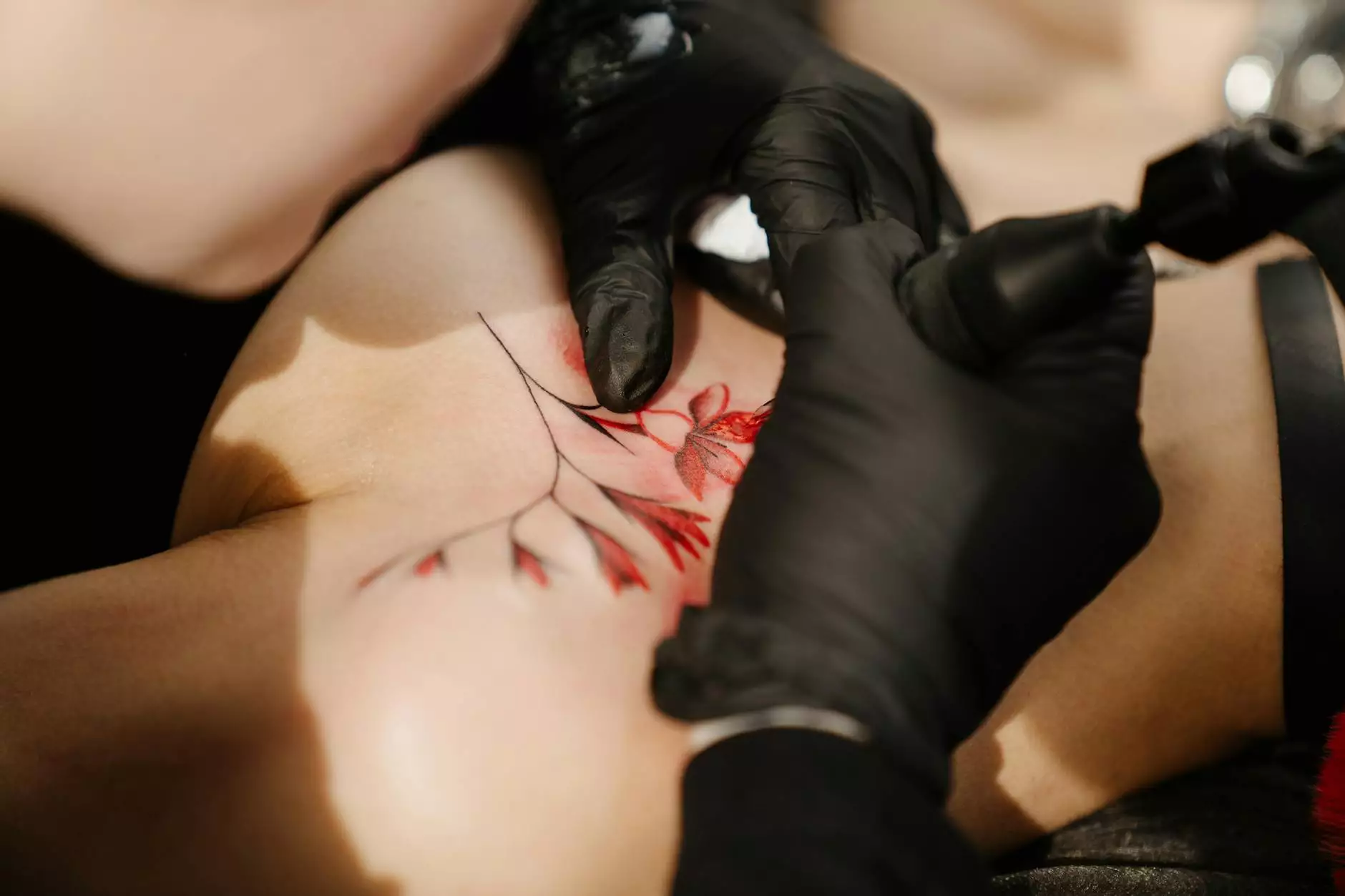
In today’s fast-paced manufacturing world, cnc machining parts factories play a pivotal role in the production of high-precision components across various industries. From automotive to aerospace and everything in between, the demand for high-quality machined parts is ever-increasing. This article delves into the intricacies of CNC machining, the operations of a typical factory, and the unparalleled advantages offered by advanced machining technologies.
Understanding CNC Machining
Computer Numerical Control (CNC) machining is a process that utilizes pre-programmed computer software to control the movement of machinery and tools. This technology is critical in achieving the precision and repeatability required in modern manufacturing. Unlike traditional machining techniques, CNC machining allows for greater accuracy and the ability to produce complex shapes and designs with ease.
The Evolution of CNC Technology
The origins of CNC machining can be traced back to the 1940s and 1950s when the first automated machine tools were developed. Over the decades, technology has progressed remarkably. Today's CNC machines are equipped with advanced features such as:
- Multi-axis control: Allowing for greater flexibility in machining complex parts.
- High-speed machining: Enabling faster production speeds and improved efficiency.
- Integration with CAD/CAM software: Streamlining the design and production processes.
Key Features of a CNC Machining Parts Factory
A typical cnc machining parts factory is equipped with various types of machines that work together to create high-quality components. Here are some of the essential features found in such factories:
Advanced Machinery
At the core of any CNC machining parts factory lies its machinery. From CNC lathes to milling machines, these machines are designed to handle various materials such as metals, plastics, and composites. The precision and flexibility of these machines enable manufacturers to produce everything from simple to highly intricate parts.
Quality Control Systems
Maintaining high-quality standards is critical in machining. CNC machining parts factories employ rigorous quality control procedures to ensure that each part meets specific tolerances. Techniques may include:
- Dimensional inspection: Using calipers, gauges, and coordinate measuring machines (CMM) to verify specifications.
- Surface finish testing: Ensuring that the surface quality meets the required standards for functionality and aesthetics.
Skilled Workforce
While CNC machines operate autonomously, they require skilled operators and technicians to program, monitor, and maintain them. A skilled workforce is essential for troubleshooting issues that may arise during machining and optimizing production processes. Training in programming and operation is vital, ensuring that employees are equipped to handle advanced machinery.
The Role of CNC Machining in Metal Fabrication
Within the metal fabrication industry, CNC machining stands out due to its incredible efficiency and accuracy. It allows fabricators to create detailed and high-quality components integral to assembly and construction. CNC machining provides several key advantages:
Enhanced Precision
One of the significant benefits of CNC machining is its unparalleled precision. Parts are manufactured to incredibly tight tolerances, sometimes within ±0.001 inches. This level of accuracy ensures that components fit correctly in assemblies, reducing the likelihood of errors and rework.
Increased Efficiency
The automation of CNC machining allows for rapid production cycles. Compared to traditional manual machining, CNC machines operate continuously, producing parts at a significantly faster rate. This efficiency contributes to lower production costs and faster turnaround times for clients.
Diverse Material Capability
CNC machining is not limited to a single material. Factories are capable of machining a variety of materials, including:
- Aluminum: Lightweight and corrosion-resistant, ideal for many applications.
- Steel: Strong and durable, commonly used in heavy machinery and structural components.
- Titanium: Known for its strength-to-weight ratio, often utilized in aerospace applications.
- Plastics: Versatile and easy to machine for a variety of consumer products.
DeepMould: Leading the Way in CNC Machining
Among the many players in the CNC machining industry, DeepMould stands out as a premier cnc machining parts factory. With a commitment to innovation, quality, and customer satisfaction, DeepMould has established itself as a leader in metal fabrication. Here are some advantages that separate DeepMould from the competition:
State-of-the-Art Technology
DeepMould invests in cutting-edge technology to enhance its capabilities continually. The integration of the latest CNC machinery and software ensures that the factory can handle complex projects efficiently while maintaining stringent quality standards.
Custom Solutions
Understanding that each client has unique needs, DeepMould offers customized machining solutions. Whether a client needs a one-off prototype or large production runs, the team works closely with customers to deliver tailored solutions that meet specific requirements.
Commitment to Sustainability
Environmental responsibility is an integral part of DeepMould's operations. The factory employs sustainable practices, such as:
- Waste Reduction: Implementing processes that minimize scrap and recycling materials.
- Energy Efficiency: Utilizing energy-efficient machinery to reduce the factory's carbon footprint.
The Future of CNC Machining
As technology advances, the future of CNC machining looks promising. Innovations such as artificial intelligence (AI) and machine learning are beginning to influence how factories operate, allowing for predictive maintenance and improved manufacturing processes. Moreover, with the rise of Industry 4.0, factories are becoming increasingly interconnected, enabling data-driven decision-making that enhances efficiency and quality.
Impact of Additive Manufacturing
Additionally, the integration of additive manufacturing, or 3D printing, with traditional CNC machining presents new opportunities. This hybrid approach enables manufacturers to create complex geometries that were previously impossible to achieve with traditional machining alone. As these technologies evolve, CNC machining parts factories like DeepMould will be at the forefront of innovation.
Conclusion
The role of a cnc machining parts factory in the modern manufacturing landscape cannot be overstated. With precision engineering at its core, CNC machining not only enhances the efficiency of production processes but also ensures the delivery of high-quality products. Companies like DeepMould exemplify the best practices in this industry, continually pushing the envelope in quality, customization, and sustainability.
As we look toward the future, it is clear that CNC machining will remain crucial in shaping the products and technologies that drive our world forward. Embracing these advancements will be essential for any manufacturing entity aiming to thrive in an ever-evolving market.