Unlocking Innovation: The Role of a Leading Plastic Prototype Manufacturer
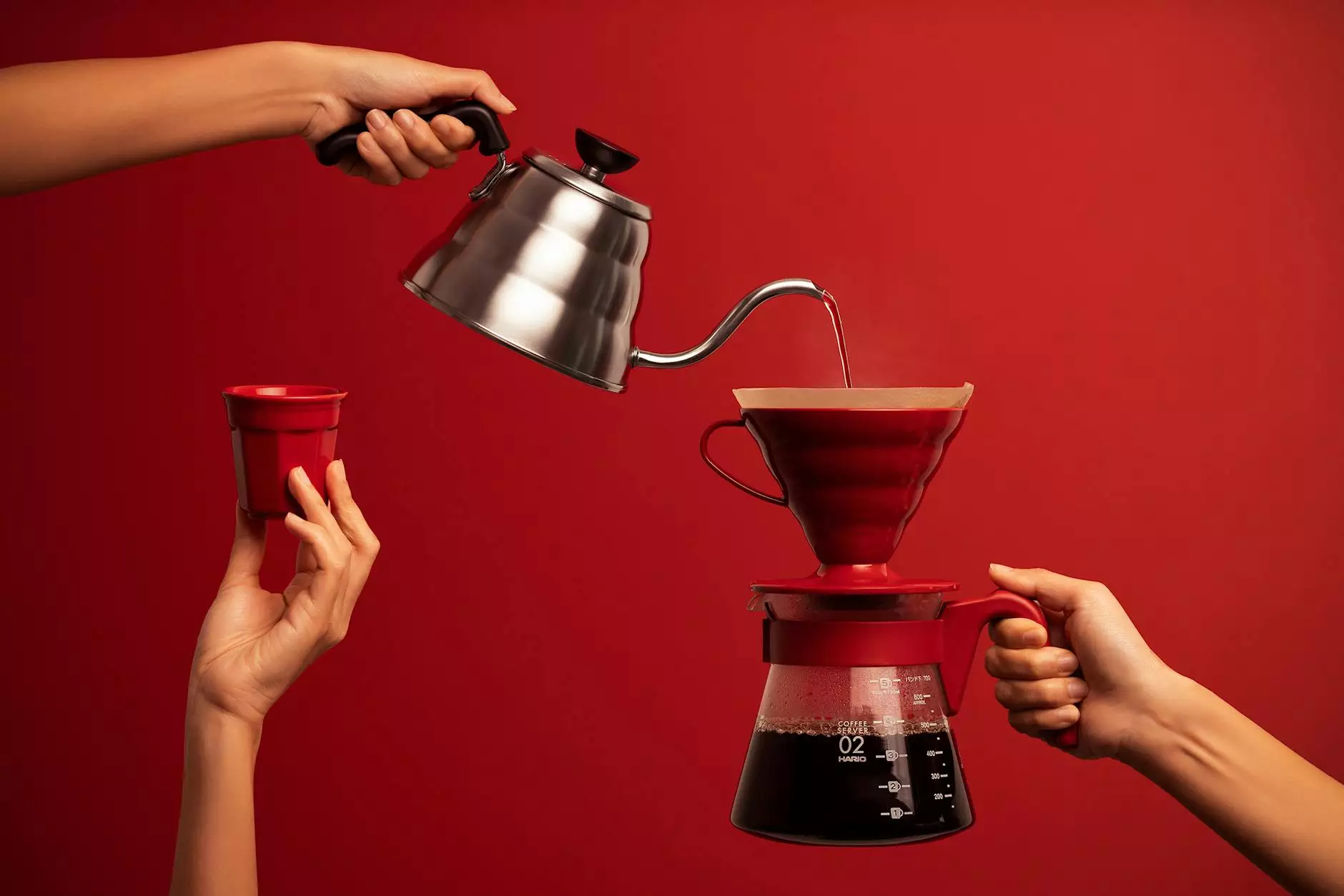
Introduction to Plastic Prototyping
In today’s fast-paced market, innovation is key to staying ahead. A plastic prototype manufacturer plays a crucial role in this ever-evolving landscape, enabling businesses to bring their ideas to life quickly and efficiently. By understanding the significance of rapid prototyping, organizations can streamline their product development processes, reduce costs, and minimize time to market.
What is Plastic Prototyping?
Plastic prototyping refers to the creation of a physical model of a product using various types of plastics. This process is integral to testing designs and functionalities before full-scale production. Prototypes serve as a tangible representation of an idea, allowing businesses to visualize the end product and make necessary adjustments. The use of a skilled plastic prototype manufacturer ensures that your prototype accurately reflects your vision, qualities, and functionality.
Benefits of Using a Plastic Prototype Manufacturer
Working with a specialized plastic prototype manufacturer offers numerous advantages, including:
- Cost Efficiency: Producing a prototype can significantly lower the costs associated with full-scale production. Manufacturers can identify flaws and make adjustments before committing to expensive materials and processes.
- Time Savings: A prototype allows for quick feedback and iteration cycles, which accelerates the development process. The faster you can iterate, the faster your product can reach the market.
- Enhanced Collaboration: Prototypes improve communication among team members, stakeholders, and potential customers, ensuring everyone is aligned with the product vision.
- Real-World Testing: Physical models can be subjected to rigorous testing, providing valuable insights into usability, performance, and functionality.
- Design Validation: A prototype allows for visual and functional evaluation, validating design choices before investing in final production.
Types of Plastic Prototyping Techniques
Plastic prototyping encompasses various techniques, each suitable for different types of projects and budgets. Here are some of the most commonly used methods:
1. 3D Printing
3D printing, or additive manufacturing, has transformed the prototyping landscape. This technique allows for the creation of complex geometries and intricate details, making it ideal for custom designs. It uses layers of material to build a model from a digital file, resulting in a quick turnaround time and cost-effective solutions.
2. CNC Machining
CNC (Computer Numerical Control) machining is a subtractive manufacturing process. It removes material from a solid block of plastic to create precise prototypes. This method is particularly well-suited for achieving high tolerances and durable parts, making it favored in industries where dimensional accuracy is paramount.
3. Injection Molding
While primarily used for mass production, injection molding can be employed for prototyping as well. This method uses an injection mold to create parts from liquid plastic, allowing for rapid production of complex shapes with excellent surface finish. It is especially beneficial when the prototype requires multiple identical units for testing.
4. Vacuum Forming
Vacuum forming is a process that involves heating a sheet of plastic until it becomes pliable and then forming it over a mold using vacuum pressure. This technique is cost-effective for producing larger parts and is often used for packaging, automotive components, and more.
Choosing the Right Plastic Prototype Manufacturer
Selecting an appropriate plastic prototype manufacturer is essential for the success of your project. Here are some critical factors to consider:
- Experience and Expertise: Look for a manufacturer with a proven track record in producing prototypes for your specific industry. Experience assures familiarity with materials and techniques.
- Capabilities: Ensure the manufacturer has the technology and resources to meet your requirements, whether that’s advanced 3D printing or high-precision CNC machining.
- Quality Control: Opt for manufacturers that implement stringent quality control measures, ensuring that prototypes are built to specifications and function as intended.
- Communication: Effective communication is critical during the prototyping process. Choose a manufacturer that values collaboration and keeps you informed at every step.
- Turnaround Time: Evaluate the manufacturer's ability to meet deadlines without sacrificing quality. Quick delivery can be crucial in fast-moving markets.
Case Studies of Successful Plastic Prototyping
To illustrate the impact of working with a plastic prototype manufacturer, consider the following case studies:
Case Study 1: Automotive Industry
A leading automotive company aimed to develop a new dashboard design that integrated advanced technology with user-friendly features. By partnering with a specialized plastic prototype manufacturer, they were able to produce multiple iterations of their design quickly. This rapid prototyping allowed the team to conduct focus groups and receive real-time feedback, leading to a final product that exceeded customer expectations.
Case Study 2: Consumer Electronics
In the competitive world of consumer electronics, a startup sought to launch a revolutionary wearable device. The design team collaborated with a plastic prototype manufacturer to produce multiple functional prototypes using 3D printing. Each prototype was rigorously tested for ergonomics and durability, ensuring that the final product was not only innovative but also user-friendly. The early investment in prototyping paid off as the product became a market leader within its category.
Future Trends in Plastic Prototyping
The landscape of plastic prototyping is constantly evolving. Here are some anticipated trends that could shape the industry in the coming years:
- Increased Automation: Automation technologies, such as AI and machine learning, are expected to streamline the prototyping process, enhancing efficiency and accuracy.
- Eco-Friendly Materials: As sustainability becomes increasingly important, the demand for biodegradable and recycled materials for prototyping is likely to rise.
- Advanced Bioprinting: Innovations in bioprinting could revolutionize industries such as healthcare by allowing for the creation of biological prototypes for medical devices and implants.
- Integration with IoT: Prototyping for smart devices that connect to the Internet of Things (IoT) will require new approaches to design and testing, paving the way for smarter prototypes.
Conclusion: The Transformative Power of a Plastic Prototype Manufacturer
In the realm of product development, a plastic prototype manufacturer is more than just a service provider; they are a critical partner in bringing your vision to life. By embracing modern prototyping techniques, businesses can enjoy reduced time to market, enhanced product quality, and ultimately, greater customer satisfaction.
Choosing the right manufacturer is vital for leveraging these benefits. It is essential to prioritize experience, capabilities, and communication. Armed with the right prototype, your business can innovate and excel in today’s dynamic market, creating products that resonate with consumers and outpace the competition.
© 2023 DeepMould, Inc. All rights reserved.