Empowering Manufacturing: The Role of Die Casting Machine Factories
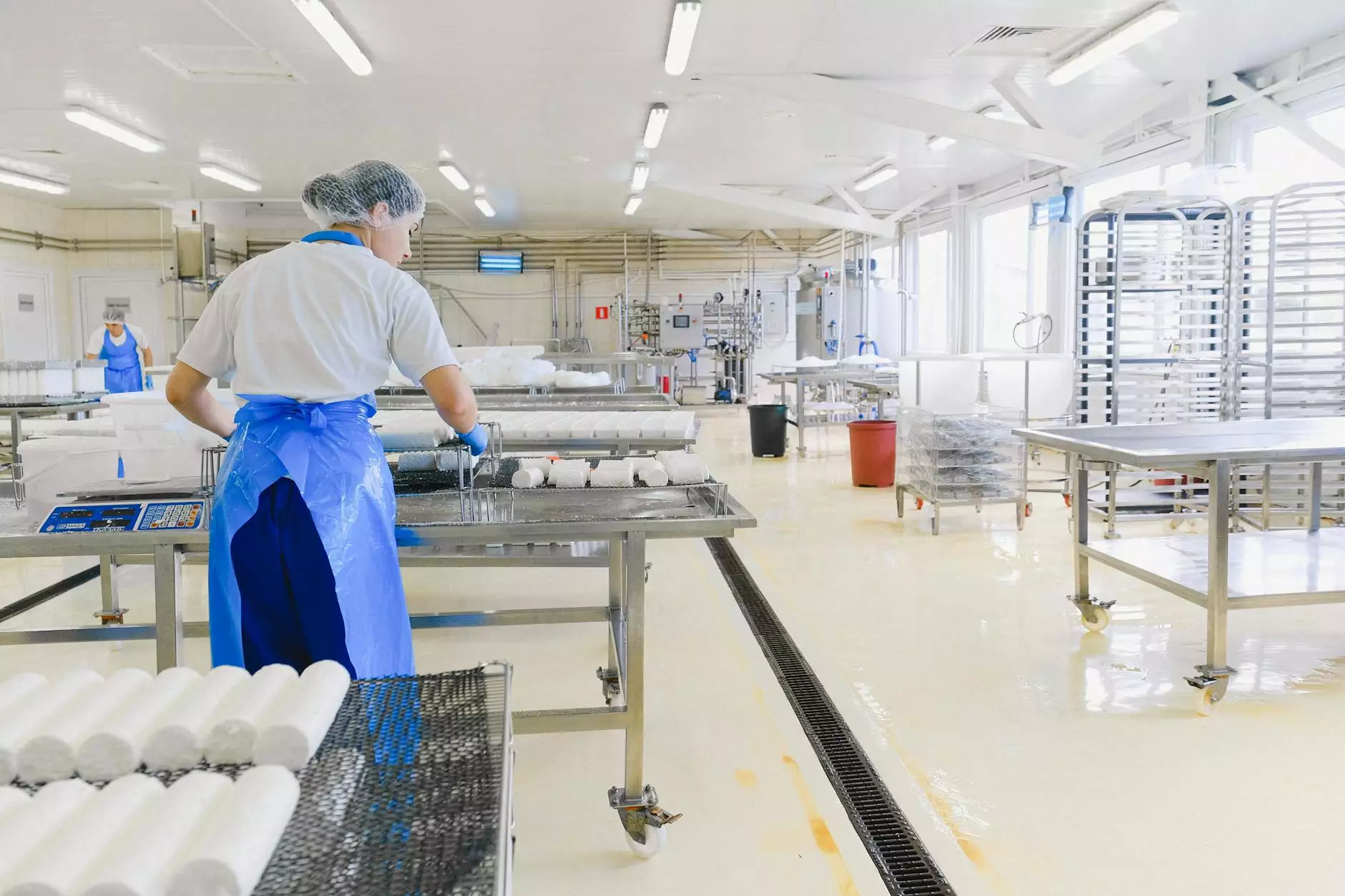
Die casting machine factories play a pivotal role in the industrial landscape, especially within the realm of metal fabrication. These factories utilize advanced technology and machinery to produce parts with precision, efficiency, and cost-effectiveness. In this comprehensive article, we will delve into the intricacies of die casting, the significance of these factories, and how they contribute to various sectors, ensuring quality and innovation in manufacturing processes.
Understanding Die Casting
Die casting is a manufacturing process that involves forcing molten metal under high pressure into a mold cavity. This cavity is known as a die, and once the metal cools and solidifies, it is ejected from the die as a finished part. The process is highly favored for producing complex geometries with superior surface finishes. In die casting machine factories, numerous benefits can be attributed to this method, including:
- High Precision: Die casting produces components with tight tolerances and intricate details.
- Cost Efficiency: The high-speed production of parts reduces labor costs and material waste.
- Versatility: Suitable for a variety of metals, including aluminum, zinc, and magnesium, die casting can cater to diverse manufacturing needs.
- Surface Finish: The quality of surface finish is superior, often requiring little to no additional machining.
The Role of Die Casting Machine Factories in Metal Fabrication
As the backbone of the manufacturing sector, die casting machine factories significantly contribute to metal fabrication. Their modern machines and processes make them vital players in producing components used in various industries:
1. Automotive Industry
The automotive industry heavily relies on die casting for producing lightweight, durable parts. These parts include engine blocks, transmission housings, and decorative components. The use of die casting allows manufacturers to achieve high productivity while maintaining stringent safety and performance standards.
2. Aerospace Sector
In aerospace, the demand for precision components is paramount. Parts produced through die casting must withstand extreme conditions, including high pressure and temperature. Die casting machine factories provide manufacturers with the capability to produce high-strength aluminum and magnesium components that are essential in this sector.
3. Consumer Electronics
The consumer electronics market is characterized by rapid innovation and high competition. With die casting, manufacturers can create intricate housings and components that enhance the aesthetic appeal while providing strength and reliability. This process allows for the production of light yet robust casings for devices like smartphones, laptops, and home appliances.
The Advantages of Using Advanced Technologies in Die Casting Machine Factories
Investments in technology enable die casting machine factories to elevate their production capabilities. The advantages of incorporating advanced technologies include:
1. Automation and Robotics
Modern die casting factories are increasingly adopting automation and robotic systems. These technologies streamline operations, reduce human error, and enhance the overall production rate. Integration of robots facilitates:
- Increased Efficiency: Robots can operate continuously, minimizing downtime associated with manual labor.
- Consistency: Automated systems ensure that each part is produced to the same high standard.
- Enhanced Safety: Automation reduces the risk associated with hazardous environments, keeping workers safe.
2. Advanced Materials and Alloys
Innovative materials and alloys specifically designed for die casting enhance the performance of the finished products. Factories can utilize:
- High-Performance Alloys: Alloys that provide better mechanical and physical properties.
- Recyclable Materials: Sustainability is a growing concern, and using recyclable metals caters to this need.
3. Quality Control Systems
Incorporating quality control mechanisms within the production line is vital. Utilizing technologies such as:
- 3D Scanning: Provides an accurate representation of parts to ensure they meet specifications.
- Machine Learning: Can predict failures or deviations in the production process, allowing for timely corrections.
Challenges Faced by Die Casting Machine Factories
Despite the numerous benefits and advancements, die casting machine factories encounter several challenges that can impact their operations:
1. Skilled Labor Shortage
The demand for skilled labor in operating advanced die casting machines is rising. Factories must invest in training programs to develop home-grown talent capable of managing modern technologies effectively. Bridging this skills gap is critical to maintaining productivity and quality.
2. Environmental Regulations
With increasing awareness of environmental issues, die casting factories must comply with stringent regulations concerning emissions and waste. The challenge lies in adopting sustainable practices while maintaining efficiency and profitability.
3. Competition and Market Dynamics
The global manufacturing landscape is becoming increasingly competitive. To stand out, die casting machine factories need to innovate continually, improve processes, and offer superior customer service to retain and attract clients.
The Future of Die Casting in Manufacturing
As the manufacturing sector evolves, so too does die casting. The future reveals promising trends that will shape the industry:
1. 3D Printing and Hybrid Manufacturing
The integration of 3D printing technologies with die casting is becoming more prevalent, allowing factories to create prototypes quickly and efficiently. This hybrid approach can reduce lead times and costs, making it a valuable strategy for manufacturers.
2. Digital Transformation
Industries are increasingly embracing digital transformation. In die casting, the use of data analytics, Internet of Things (IoT), and smart manufacturing will enhance operational efficiency and customer satisfaction. The ability to monitor machines in real-time allows for predictive maintenance and improved decision-making processes.
3. Sustainability Initiatives
With a growing emphasis on sustainable manufacturing practices, die casting machine factories will explore ways to minimize waste and energy consumption. This might include adopting more eco-friendly materials, improving recycling processes, or investing in energy-efficient machinery. Going green is not only beneficial for the planet; it also appeals to environmentally conscious consumers and can reduce operational costs.
Conclusion
In summary, die casting machine factories are integral to the metal fabrication industry, providing significant advantages through advanced technologies and efficient production processes. As they continue to innovate and adapt to changing market demands and environmental concerns, these factories will play a crucial role in driving the future of manufacturing. By focusing on quality, efficiency, and sustainability, die casting machine factories can not only survive but thrive in the global marketplace.
Considering the ongoing advancements and the increasing demand across various sectors, partnering with a reputable die casting machine factory like DeepMould can provide manufacturers with a competitive edge, ensuring that they are equipped to meet the challenges of tomorrow.